【壓縮機網(wǎng)】分析了熱噴涂技術(shù)在往復(fù)壓縮機行業(yè)上的應(yīng)用,利用熱噴涂技術(shù)對零件表面進行處理,改善表面耐磨性能,有效地延長零件使用壽命;對機械零件的磨損進行有效的修復(fù),克服傳統(tǒng)修復(fù)的不足,發(fā)揮其獨特的修復(fù)優(yōu)勢。
引言
熱噴涂技術(shù)誕生于20世紀初期,經(jīng)過近一個世紀的發(fā)展,從簡單的工藝技術(shù)發(fā)展成集機械學、材料科學、熱動力學、高新技術(shù)和生物工程等專業(yè)為一體的完整的工業(yè)體系,已經(jīng)在先進的制造技術(shù)中占有舉足輕重的位置。從鋼鐵零部件的抗磨、耐蝕,再到能起到特殊防護功能的涂層, 從中熱噴涂技術(shù)具備其他一些技術(shù)所不具備的特殊作用,現(xiàn)已在航空、航天、船舶、機械、石化、汽車、模具領(lǐng)域廣泛應(yīng)用。
當前國家提倡節(jié)能減排、低能耗、高效率,對此我公司自2005年引進熱噴涂這項實用新技術(shù)。目前已經(jīng)應(yīng)用在往復(fù)壓縮機的生產(chǎn)制造過程中,在設(shè)備零件修復(fù)方面大量使用,對一些價值高昂的零件的修復(fù)再利用,節(jié)省了大量的資金,同時也為用戶的裝置恢復(fù)生產(chǎn)節(jié)省了大量的時間;同時因該技術(shù)的應(yīng)用,對新產(chǎn)品制造中零件的強化工藝和制造工藝改變起到了極大促進作用,使其在很大程度上增加壽命和效率,節(jié)省原材料、節(jié)省功耗、提高效率,z*主要的是能降低成本,十分吻合我國現(xiàn)行的經(jīng)濟政策。
熱噴涂技術(shù)簡介
一直以來零件表面防護和強化始終是一個探討很熱烈的課題,而熱噴涂技術(shù)的應(yīng)用,更加將其拓展開來,熱噴涂技術(shù)從原理上講是指用熱源(像電弧、等離子弧、燃燒火焰等),將絲狀或粉末狀的非金屬和金屬材料經(jīng)過高溫熔解或半熔解狀態(tài), 借助熱源本身的動力或者高速高壓的氣流將其霧化成顆粒狀態(tài),形成一束粒子噴霧,以特定的速度噴射擊打在經(jīng)過事先處理過的基體表面,與基體材料結(jié)合而形成一種附著力很強不亞于基體本身材料附著力的涂層,根據(jù)噴涂材料的不同可以形成耐磨、抗腐蝕等各種功能的表面涂層,其原理圖如圖1。
常見的噴涂工藝大概有6種,分別為等離子噴涂、電弧噴涂、火焰粉末噴涂、火焰絲材噴涂、超音速火焰噴涂、低溫超音速火焰噴涂。每一種方法都有各自的優(yōu)點與局限性,其應(yīng)用范圍也各有不同,表1列舉了這些方法的基本工藝特點。通過熱噴涂技術(shù)可以在材料表面形成耐磨涂層、防腐涂層、抗高溫涂層、耐氧化涂層、導(dǎo)電涂層、絕緣涂層等各種功能的涂層。
在往復(fù)壓縮機行業(yè)上的應(yīng)用
在往復(fù)壓縮機行業(yè)中,熱噴涂技術(shù)主要應(yīng)用于零部件的表面耐磨(防腐)強化涂層的制造及修復(fù),零部件尺寸恢復(fù)等方面。
1.曲軸的修復(fù)
曲軸是往復(fù)壓縮機的主要部件,常由于潤滑系統(tǒng)故障,致使主軸瓦及連桿瓦燒毀,對曲軸的軸徑和拐徑表面造成拉傷或燒傷,出現(xiàn)整圈的溝狀劃痕或裂紋,燒傷嚴重就會出現(xiàn)龜裂狀遍布整個徑面的微小裂紋。將表面的劃痕和裂紋磨削處理去掉后,探傷檢測后剩余軸徑盡管完好,尺寸卻小了很多,已不能繼續(xù)直接使用。針對曲軸這種損傷后常規(guī)的處理辦法是直接將軸徑的損傷磨掉,重新配加厚軸瓦。如果出現(xiàn)幾次事故后,一是軸徑尺寸會越修越小,z*后導(dǎo)致曲軸的安全系數(shù)不夠報廢;二是軸瓦的厚度尺寸就會出現(xiàn)很多種不利于壓縮機的維護和軸瓦的采購。針對這種情況,可采用電弧噴涂技術(shù)對損壞的曲軸進行修復(fù)。修復(fù)后恢復(fù)至曲軸原尺寸,保證了軸瓦的通用性,不用重新采購加厚瓦,且便于維護和采購管理。如果再次出現(xiàn)損傷后,可以將涂層磨去重新噴涂,保證曲軸的長期使用性。
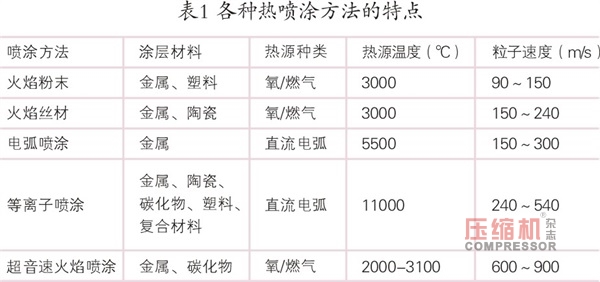
往復(fù)壓縮機曲軸是一個尺寸精度高,整體形位公差要求嚴格的大型零件,修復(fù)的過程中要嚴格保證曲軸修復(fù)徑面的尺寸以及整體軸系的形位公差。常規(guī)的曲軸材料都是碳鋼和合金鋼,其性能和適應(yīng)性非常適合熱噴涂工藝??刂仆繉咏Y(jié)合力在45 MPa左右,保證了一定的孔隙率。工作時潤滑油進入微孔,保證徑面上一定的含油量,能很容易形成油膜,故此金屬噴涂層具備了良好的耐磨效果。噴涂時在氣流的作用下曲軸的溫升不會增加很多,一般能夠控制在40℃上下,對曲軸本體的金相組織和變形可以忽略不計。其加工過程如下:
粗磨徑面→徑面除塵除油噴砂處理→噴底層涂層→噴涂耐磨涂層→精磨涂層表面至要求尺寸精度。
曲軸的安全系數(shù)較大,一般根據(jù)損傷情況大概磨去直徑尺寸1~1.5 mm左右,不會影響曲軸的安全性。粗磨去掉軸徑表面損傷痕跡后,磁粉或著色檢測無裂紋后,可直接進行修復(fù)。修復(fù)后的表面,應(yīng)均勻無裂紋、夾雜等缺陷,硬度在HRC45以上,超過原材料本身的硬度,且耐磨性有較大提升。圖2為中石化揚子石化進口4M80壓縮機曲軸修復(fù)前、后的對比圖。
2.活塞桿摩擦面修復(fù)及噴涂碳化鎢耐磨涂層
活塞桿是往復(fù)壓縮機的重要零件,在設(shè)備進行過程中摩擦面不斷與填料摩擦,易造成活塞桿的磨損和劃傷。
活塞桿的常規(guī)材料有38CrMoAlA、42CrMo、20Cr13、17-4PH (僅用于H2S腐蝕環(huán)境)等等,與曲軸修復(fù)工藝一樣,也可采用電弧噴涂技術(shù)對損壞的活塞桿進行常規(guī)修復(fù)。
同時還可以采用超音速火焰噴涂工藝,噴涂碳化鎢耐磨涂層,可以極大地提高活塞桿的耐磨性。經(jīng)過驗證,這種耐磨涂層的結(jié)合強度高于70MPa,經(jīng)過鏡面拋光后,粗糙度可達到Ra0.1,其使用壽命為高頻淬火活塞桿的4倍。相對應(yīng)的摩擦面(填料部位)的使用壽命也大幅提高。這種熱噴涂工藝,既可用于新活塞桿的表面強化,也可用于舊活塞桿修復(fù),加工過程中基體金相組織不發(fā)生改變,保持原有力學性能;加工過程零件溫度低,不發(fā)生變形;適用性好,幾乎不受零件尺寸限制;具有良好的可拋光性;工藝簡單,生產(chǎn)周期短。其工藝過程如下:粗磨表面→表面預(yù)處理→噴涂耐磨涂層→涂層的機械加工(磨削加工)→拋光。
十字頭(滑履)噴涂巴氏合金涂層
巴氏合金是滑動軸承內(nèi)表面的涂層材料,以前和現(xiàn)在的常規(guī)工藝都是采用手工氣焊將巴氏合金一點點融化后,一點點的滴抹在十字頭滑履表面。但在生產(chǎn)過程中,采用這種常規(guī)的工藝在加工車削后經(jīng)常發(fā)現(xiàn)巴氏合金涂層有氣孔,更甚者因加工車削導(dǎo)致脫層、開裂等溶解貼合不完全的缺陷,遇到這些情況,z*后只能重新掛巴氏合金。
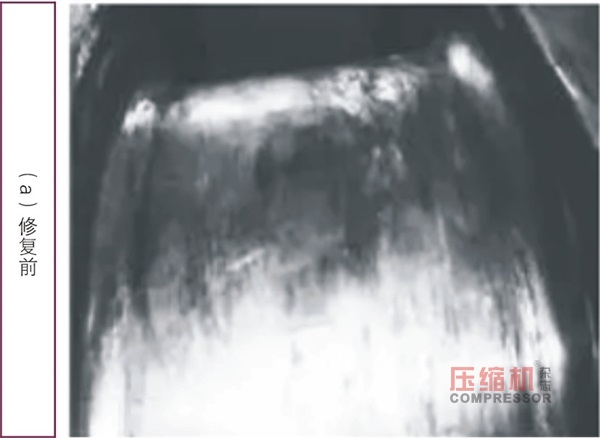
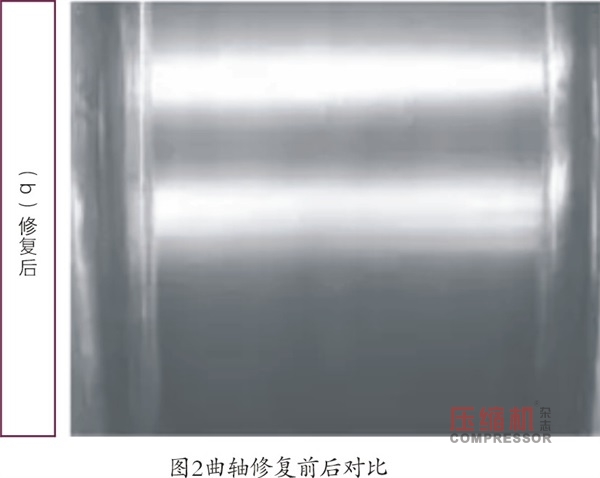
這樣對產(chǎn)品的質(zhì)量和加工周期都會產(chǎn)生很大的不穩(wěn)定性。采用電弧噴涂工藝制造巴氏合金涂層可有效避免上述缺點,并且生產(chǎn)效率高,成本低,質(zhì)量穩(wěn)定容易控制。另外,采用熱噴涂技術(shù)噴涂的的巴氏合金涂層與澆鑄組織相比,涂層很薄,分子顆粒更細小,結(jié)合力很強,保證一定的孔隙率使其具有良好的儲油效果,在摩擦副之間很容易形成油膜,其耐磨性較傳統(tǒng)澆鑄工藝提高很多倍,經(jīng)使用驗證其使用壽命大概能提高2倍左右。其制造過程:粗車滑履表面→滑履表面除塵除油噴砂處理→噴涂粘接底層→噴涂巴氏合金涂層→車削加工。
經(jīng)濟效益分析
以曲軸修復(fù)為例,購買一根4拐50t活塞力的曲軸的平均價格約為50萬元,周期約為2~3個月,而采用熱噴涂技術(shù)修復(fù)一根曲軸的價格約為2~6萬元,可以節(jié)約資金達90%~95%,費用極低,周期約為3天,更重要的是節(jié)約了能源和資源。采用熱噴涂工藝修復(fù)零件,具有及時性,減少了停產(chǎn)損失,無形中也給企業(yè)增加了效益。
再以噴涂碳化鎢涂層活塞桿為例,噴涂碳化鎢活塞桿的價格約為普通高頻淬火活塞桿的2倍,但是其使用壽命能達到普通活塞桿的4倍,延長了活塞桿的使用周期,節(jié)省了采購成本,同時給設(shè)備安全穩(wěn)定運行帶來便利。
結(jié)語
熱噴涂技術(shù)在往復(fù)壓縮機行業(yè)經(jīng)歷了20多年的發(fā)展,并逐漸被市場所認可。通過對壓縮機零件的強度計算,在滿足安全的前提下,作為零部件的尺寸修復(fù)、滿足和提升各種性能的要求擁有不可代替的優(yōu)勢。隨著技術(shù)的發(fā)展,熱噴涂技術(shù)在往復(fù)壓縮機行業(yè)的應(yīng)用能否進一步拓展,一些新型的材料能否在壓縮機行業(yè)得到應(yīng)用,需要進一步的實驗驗證和系統(tǒng)的理論研究。
參考文獻
[1] 張平.熱噴涂材料[M].北京:國防工業(yè)出版社,2006.[2] 吳子健.熱噴涂技術(shù)與應(yīng)用[M].北京:機械工業(yè)出版社,2006.
[3] 楊中元.鎳鋁復(fù)合絲和鎳鋁合金絲及其涂層[J].材料工程,2002,2.
[4] 張忠禮,等. 電弧噴涂錫基巴氏合金涂層的組織與性能
[J].焊接學報,2010,4.
【壓縮機網(wǎng)】分析了熱噴涂技術(shù)在往復(fù)壓縮機行業(yè)上的應(yīng)用,利用熱噴涂技術(shù)對零件表面進行處理,改善表面耐磨性能,有效地延長零件使用壽命;對機械零件的磨損進行有效的修復(fù),克服傳統(tǒng)修復(fù)的不足,發(fā)揮其獨特的修復(fù)優(yōu)勢。

引言
熱噴涂技術(shù)誕生于20世紀初期,經(jīng)過近一個世紀的發(fā)展,從簡單的工藝技術(shù)發(fā)展成集機械學、材料科學、熱動力學、高新技術(shù)和生物工程等專業(yè)為一體的完整的工業(yè)體系,已經(jīng)在先進的制造技術(shù)中占有舉足輕重的位置。從鋼鐵零部件的抗磨、耐蝕,再到能起到特殊防護功能的涂層, 從中熱噴涂技術(shù)具備其他一些技術(shù)所不具備的特殊作用,現(xiàn)已在航空、航天、船舶、機械、石化、汽車、模具領(lǐng)域廣泛應(yīng)用。
當前國家提倡節(jié)能減排、低能耗、高效率,對此我公司自2005年引進熱噴涂這項實用新技術(shù)。目前已經(jīng)應(yīng)用在往復(fù)壓縮機的生產(chǎn)制造過程中,在設(shè)備零件修復(fù)方面大量使用,對一些價值高昂的零件的修復(fù)再利用,節(jié)省了大量的資金,同時也為用戶的裝置恢復(fù)生產(chǎn)節(jié)省了大量的時間;同時因該技術(shù)的應(yīng)用,對新產(chǎn)品制造中零件的強化工藝和制造工藝改變起到了極大促進作用,使其在很大程度上增加壽命和效率,節(jié)省原材料、節(jié)省功耗、提高效率,z*主要的是能降低成本,十分吻合我國現(xiàn)行的經(jīng)濟政策。
熱噴涂技術(shù)簡介
一直以來零件表面防護和強化始終是一個探討很熱烈的課題,而熱噴涂技術(shù)的應(yīng)用,更加將其拓展開來,熱噴涂技術(shù)從原理上講是指用熱源(像電弧、等離子弧、燃燒火焰等),將絲狀或粉末狀的非金屬和金屬材料經(jīng)過高溫熔解或半熔解狀態(tài), 借助熱源本身的動力或者高速高壓的氣流將其霧化成顆粒狀態(tài),形成一束粒子噴霧,以特定的速度噴射擊打在經(jīng)過事先處理過的基體表面,與基體材料結(jié)合而形成一種附著力很強不亞于基體本身材料附著力的涂層,根據(jù)噴涂材料的不同可以形成耐磨、抗腐蝕等各種功能的表面涂層,其原理圖如圖1。

常見的噴涂工藝大概有6種,分別為等離子噴涂、電弧噴涂、火焰粉末噴涂、火焰絲材噴涂、超音速火焰噴涂、低溫超音速火焰噴涂。每一種方法都有各自的優(yōu)點與局限性,其應(yīng)用范圍也各有不同,表1列舉了這些方法的基本工藝特點。通過熱噴涂技術(shù)可以在材料表面形成耐磨涂層、防腐涂層、抗高溫涂層、耐氧化涂層、導(dǎo)電涂層、絕緣涂層等各種功能的涂層。
在往復(fù)壓縮機行業(yè)上的應(yīng)用
在往復(fù)壓縮機行業(yè)中,熱噴涂技術(shù)主要應(yīng)用于零部件的表面耐磨(防腐)強化涂層的制造及修復(fù),零部件尺寸恢復(fù)等方面。
1.曲軸的修復(fù)
曲軸是往復(fù)壓縮機的主要部件,常由于潤滑系統(tǒng)故障,致使主軸瓦及連桿瓦燒毀,對曲軸的軸徑和拐徑表面造成拉傷或燒傷,出現(xiàn)整圈的溝狀劃痕或裂紋,燒傷嚴重就會出現(xiàn)龜裂狀遍布整個徑面的微小裂紋。將表面的劃痕和裂紋磨削處理去掉后,探傷檢測后剩余軸徑盡管完好,尺寸卻小了很多,已不能繼續(xù)直接使用。針對曲軸這種損傷后常規(guī)的處理辦法是直接將軸徑的損傷磨掉,重新配加厚軸瓦。如果出現(xiàn)幾次事故后,一是軸徑尺寸會越修越小,z*后導(dǎo)致曲軸的安全系數(shù)不夠報廢;二是軸瓦的厚度尺寸就會出現(xiàn)很多種不利于壓縮機的維護和軸瓦的采購。針對這種情況,可采用電弧噴涂技術(shù)對損壞的曲軸進行修復(fù)。修復(fù)后恢復(fù)至曲軸原尺寸,保證了軸瓦的通用性,不用重新采購加厚瓦,且便于維護和采購管理。如果再次出現(xiàn)損傷后,可以將涂層磨去重新噴涂,保證曲軸的長期使用性。
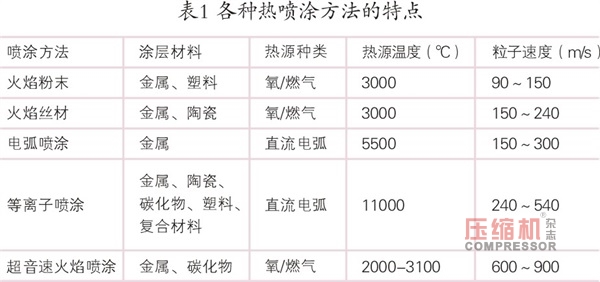
往復(fù)壓縮機曲軸是一個尺寸精度高,整體形位公差要求嚴格的大型零件,修復(fù)的過程中要嚴格保證曲軸修復(fù)徑面的尺寸以及整體軸系的形位公差。常規(guī)的曲軸材料都是碳鋼和合金鋼,其性能和適應(yīng)性非常適合熱噴涂工藝??刂仆繉咏Y(jié)合力在45 MPa左右,保證了一定的孔隙率。工作時潤滑油進入微孔,保證徑面上一定的含油量,能很容易形成油膜,故此金屬噴涂層具備了良好的耐磨效果。噴涂時在氣流的作用下曲軸的溫升不會增加很多,一般能夠控制在40℃上下,對曲軸本體的金相組織和變形可以忽略不計。其加工過程如下:
粗磨徑面→徑面除塵除油噴砂處理→噴底層涂層→噴涂耐磨涂層→精磨涂層表面至要求尺寸精度。
曲軸的安全系數(shù)較大,一般根據(jù)損傷情況大概磨去直徑尺寸1~1.5 mm左右,不會影響曲軸的安全性。粗磨去掉軸徑表面損傷痕跡后,磁粉或著色檢測無裂紋后,可直接進行修復(fù)。修復(fù)后的表面,應(yīng)均勻無裂紋、夾雜等缺陷,硬度在HRC45以上,超過原材料本身的硬度,且耐磨性有較大提升。圖2為中石化揚子石化進口4M80壓縮機曲軸修復(fù)前、后的對比圖。
2.活塞桿摩擦面修復(fù)及噴涂碳化鎢耐磨涂層
活塞桿是往復(fù)壓縮機的重要零件,在設(shè)備進行過程中摩擦面不斷與填料摩擦,易造成活塞桿的磨損和劃傷。
活塞桿的常規(guī)材料有38CrMoAlA、42CrMo、20Cr13、17-4PH (僅用于H2S腐蝕環(huán)境)等等,與曲軸修復(fù)工藝一樣,也可采用電弧噴涂技術(shù)對損壞的活塞桿進行常規(guī)修復(fù)。
同時還可以采用超音速火焰噴涂工藝,噴涂碳化鎢耐磨涂層,可以極大地提高活塞桿的耐磨性。經(jīng)過驗證,這種耐磨涂層的結(jié)合強度高于70MPa,經(jīng)過鏡面拋光后,粗糙度可達到Ra0.1,其使用壽命為高頻淬火活塞桿的4倍。相對應(yīng)的摩擦面(填料部位)的使用壽命也大幅提高。這種熱噴涂工藝,既可用于新活塞桿的表面強化,也可用于舊活塞桿修復(fù),加工過程中基體金相組織不發(fā)生改變,保持原有力學性能;加工過程零件溫度低,不發(fā)生變形;適用性好,幾乎不受零件尺寸限制;具有良好的可拋光性;工藝簡單,生產(chǎn)周期短。其工藝過程如下:粗磨表面→表面預(yù)處理→噴涂耐磨涂層→涂層的機械加工(磨削加工)→拋光。
十字頭(滑履)噴涂巴氏合金涂層
巴氏合金是滑動軸承內(nèi)表面的涂層材料,以前和現(xiàn)在的常規(guī)工藝都是采用手工氣焊將巴氏合金一點點融化后,一點點的滴抹在十字頭滑履表面。但在生產(chǎn)過程中,采用這種常規(guī)的工藝在加工車削后經(jīng)常發(fā)現(xiàn)巴氏合金涂層有氣孔,更甚者因加工車削導(dǎo)致脫層、開裂等溶解貼合不完全的缺陷,遇到這些情況,z*后只能重新掛巴氏合金。
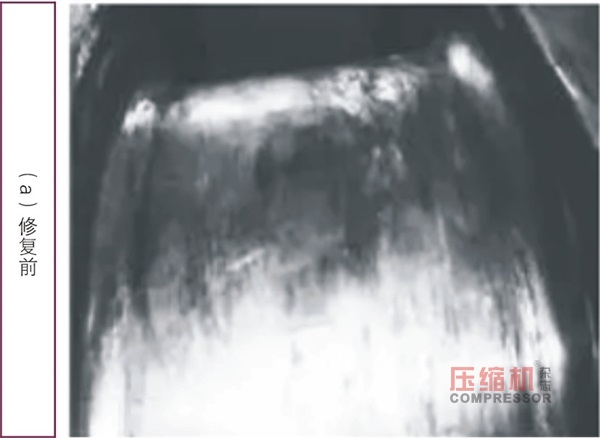
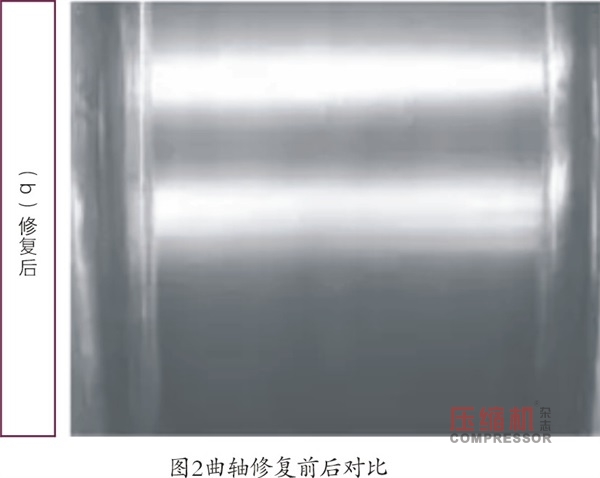
這樣對產(chǎn)品的質(zhì)量和加工周期都會產(chǎn)生很大的不穩(wěn)定性。采用電弧噴涂工藝制造巴氏合金涂層可有效避免上述缺點,并且生產(chǎn)效率高,成本低,質(zhì)量穩(wěn)定容易控制。另外,采用熱噴涂技術(shù)噴涂的的巴氏合金涂層與澆鑄組織相比,涂層很薄,分子顆粒更細小,結(jié)合力很強,保證一定的孔隙率使其具有良好的儲油效果,在摩擦副之間很容易形成油膜,其耐磨性較傳統(tǒng)澆鑄工藝提高很多倍,經(jīng)使用驗證其使用壽命大概能提高2倍左右。其制造過程:粗車滑履表面→滑履表面除塵除油噴砂處理→噴涂粘接底層→噴涂巴氏合金涂層→車削加工。
經(jīng)濟效益分析
以曲軸修復(fù)為例,購買一根4拐50t活塞力的曲軸的平均價格約為50萬元,周期約為2~3個月,而采用熱噴涂技術(shù)修復(fù)一根曲軸的價格約為2~6萬元,可以節(jié)約資金達90%~95%,費用極低,周期約為3天,更重要的是節(jié)約了能源和資源。采用熱噴涂工藝修復(fù)零件,具有及時性,減少了停產(chǎn)損失,無形中也給企業(yè)增加了效益。
再以噴涂碳化鎢涂層活塞桿為例,噴涂碳化鎢活塞桿的價格約為普通高頻淬火活塞桿的2倍,但是其使用壽命能達到普通活塞桿的4倍,延長了活塞桿的使用周期,節(jié)省了采購成本,同時給設(shè)備安全穩(wěn)定運行帶來便利。
結(jié)語
熱噴涂技術(shù)在往復(fù)壓縮機行業(yè)經(jīng)歷了20多年的發(fā)展,并逐漸被市場所認可。通過對壓縮機零件的強度計算,在滿足安全的前提下,作為零部件的尺寸修復(fù)、滿足和提升各種性能的要求擁有不可代替的優(yōu)勢。隨著技術(shù)的發(fā)展,熱噴涂技術(shù)在往復(fù)壓縮機行業(yè)的應(yīng)用能否進一步拓展,一些新型的材料能否在壓縮機行業(yè)得到應(yīng)用,需要進一步的實驗驗證和系統(tǒng)的理論研究。
參考文獻
[1] 張平.熱噴涂材料[M].北京:國防工業(yè)出版社,2006.[2] 吳子健.熱噴涂技術(shù)與應(yīng)用[M].北京:機械工業(yè)出版社,2006.
[3] 楊中元.鎳鋁復(fù)合絲和鎳鋁合金絲及其涂層[J].材料工程,2002,2.
[4] 張忠禮,等. 電弧噴涂錫基巴氏合金涂層的組織與性能
[J].焊接學報,2010,4.
網(wǎng)友評論
條評論
最新評論